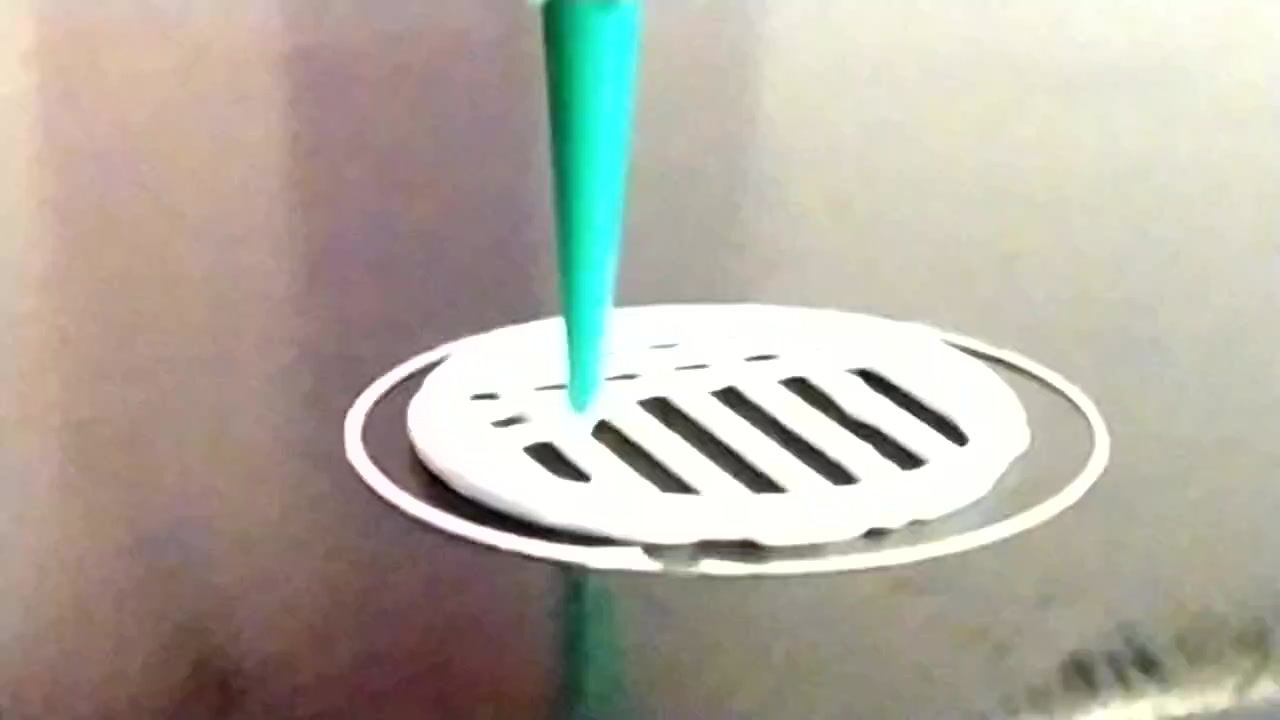
building up!!
Tissue engineering has been defined as the science of persuading the body to regenerate or repair tissues that fail to regenerate or heal spontaneously. The main approach in tissue engineering utilizes cells, signals and scaffolds for the design and construction of biological substitutes that should result in tissue regeneration. Additive manufacturing (AM) techniques are becoming the techniques of choice for the development of scaffolds in tissue engineering (TE). The main advantage of AM is the ability of designing geometrical parameters of the scaffolds such as pore size, pore strut thickness, pore interconnectivity and pore morphology in advance, and the potential to tailor and scale the manufacturing of scaffolds to each experimental model or patient

Influence of Hydroxyapatite and Gelatin Content on Crosslinking Dynamics and HDFn Cell Viability in Alginate Bioinks for 3D Bioprinting​
This study investigates how varying concentrations of hydroxyapatite (OHAp) and the addition of gelatin influence the ionic crosslinking time of alginate-based bioinks, as well as the shear stress experienced by neonatal human dermal fibroblasts (HDFn) during extrusion. These factors are crucial for validating bioinks and developing viable 3D bioprinted models. Four bioink formulations were created with a 50/50 ratio of alginate to gelatin, incorporating different calcium phosphate concentrations (0%, 1%, 5%, and 10%). The bioink compositions were confirmed via Fourier Transform Infrared (FT-IR) spectroscopy, and rheological analyses evaluated their pseudoplastic behavior, printability limits, and crosslinking times. The results indicated a notable increase in the consistency index (k) from 0.32 for the 0% OHAp formulation to 0.48 for the 10% OHAp formulation, suggesting improved viscoelastic properties. The elastic modulus recovery after crosslinking rose significantly from 245 Pa to 455 Pa. HDFn experienced a shear stress of up to 1.5436 Pa at the tip during extrusion with the HDFn-ALG5-GEL5-OHAp10 bioinks, calculated at a shear rate as low as 2 s−1. Viability assays confirmed over 70% cell viability 24 h post-extrusion and 92% viability after 7 days for the 10% OHAp formulation, highlighting the potential of hydroxyapatite-enhanced bioinks in tissue engineering applications.

Assessment of a PCL-3D printing-Dental Pulp Stem Cells triplet for bone engineering: an in vitro study.
​
Raúl Rosales-Ibáñez, Nieves Cubo-Mateo, Amairany Rodríguez-Navarrete, Arely M González-González, Tomás E Villamar-Duque, Leticia O Flores-Sánchez, Luis M Rodríguez-Lorenzo
​
in: Polymers 2021, 13(7), 1154; https://doi.org/10.3390/polym13071154
http://hdl.handle.net/10261/236626
This is a great place to add a tagline.
The search of suitable combinations of stem cells, biomaterials and scaffolds manufacturing methods have become a major focus of research for bone engineering. The aim of this study was to test the potential of dental pulp stem cells to attach, proliferate, mineralize and differentiate on 3D printed polycaprolactone (PCL) scaffolds. A 100% pure Mw: 84500 ± 1000 PCL was selected. 19 5x10x5 mm parallelepiped scaffolds were designed as a wood-pilled structure composed of 20 layers of 250 μm in height, in a non-alternate order ([0,0,0,90,90,90º]). 3D printing was made at 170ºC. Swine dental pulp stem cells (DPSCs) were extracted from lower lateral incisors of swine and cultivated until the cells reached 80% confluence. The third passage was used for seeding on 23 the scaffolds. Phenotype of cells was determined by flow Cytometry. Live and dead, Alamar blueTM, von Kossa and alizarin red staining assays were performed. Scaffolds with 290+30μm strand diameter, 938+80μm pores in the axial direction and 689+13μm pores in the lateral direction were manufactured. Together, cell viability tests, von Kossa and Alizarin red staining indicate the ability of the printed scaffolds to support DPSCs attachment, proliferation and enable differentiation followed by mineralization. The selected material-processing technique-cell line (PCL-3D printing-DPSCs) triplet can be though to be used for further modelling and preclinical experiments in bone engineering studies.
​
​
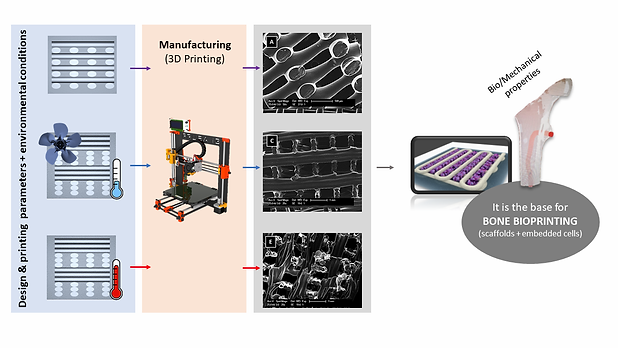

Design of Thermoplastic 3D-Printed Scaffolds for Bone Tissue Engineering: Influence of Parameters of “Hidden” Importance in the Physical Properties of Scaffolds
​
Nieves Cubo-Mateo, Luis M. Rodríguez-Lorenzo
​
Polymers 2020, 12(7), 1546
DOI:10.3390/polym12071546
http://hdl.handle.net/10261/216708
Additive manufacturing (AM) techniques are becoming the approaches of choice for the construction of scaffolds in tissue engineering. However, the development of 3D printing in this field brings unique challenges, which must be accounted for in the design of experiments. The common printing process parameters must be considered as important factors in the design and quality of final 3D-printed products. In this work, we study the influence of some parameters in the design and fabrication of PCL scaffolds, such as the number and orientation of layers, but also others of “hidden” importance, such as the cooling down rate while printing, or the position of the starting point in each layer. These factors can have an important impact oin the final porosity and mechanical performance of the scaffolds. A pure polycaprolactone filament was used. Three different configurations were selected for the design of the internal structure of the scaffolds: a solid one with alternate layers (solid) (0°, 90°), a porous one with 30% infill and alternate layers (ALT) (0°, 90°) and a non-alternated configuration consisting in printing three piled layers before changing the orientation (n-ALT) (0°, 0°, 0°, 90°, 90°, 90°). The nozzle temperature was set to 172 °C for printing and the build plate to 40 °C. Strand diameters of 361 ± 26 µm for room temperature cooling down and of 290 ± 30 µm for forced cooling down, were obtained. A compression elastic modulus of 2.12 ± 0.31 MPa for n-ALT and 8.58 ± 0.14 MPa for ALT scaffolds were obtained. The cooling down rate has been observed as an important parameter for the final characteristics of the scaffold